ظهور ابزارهای ماشین CNC جلوه ای از پیشرفت بزرگ در صنعت است. این بهتر می تواند مشکلات پردازش قطعات کثیف ، ریز ، کوچک و پردازش قابل تغییر را حل کند. این یک ابزار ماشین حساس و کارآمد است. هنگامی که برنامه نویسان برای پردازش از دستگاه های CNC استفاده می کنند ، ابتدا باید فرآیند را تجزیه و تحلیل کنند. با توجه به اطلاعات ، شکل عمومی ، دقت ماشینکاری و غیره از قطعه کار که باید پردازش شود ، یک ابزار ماشین مناسب انتخاب می شود ، برنامه پردازش تهیه می شود ، توالی پردازش قطعات تأیید می شود ، ابزارهای مورد استفاده در هر فرآیند ، فیکسچر و مقدار برش و غیره
1. انتخاب معقول ابزارهای ماشین
هنگام ماشینکاری قطعات روی یک دستگاه CNC ، به طور کلی دو موقعیت وجود دارد.
وضعیت اول: یک الگوی جزئی و یک خالی وجود دارد و یک ابزار CNC مناسب برای پردازش قسمت باید انتخاب شود.
وضعیت دوم: در حال حاضر یک دستگاه ماشین CNC وجود دارد و لازم است قطعات مناسب برای پردازش روی ابزار را انتخاب کنید.
صرف نظر از وضعیت ، عوامل اصلی که باید در نظر بگیرید اطلاعات و نوع خالی ، میزان اختلال در شکل عمومی قسمت ، اندازه مقیاس ، دقت پردازش ، تعداد قطعات و عملیات حرارتی است. الزامات. به طور خلاصه ، سه نکته وجود دارد:
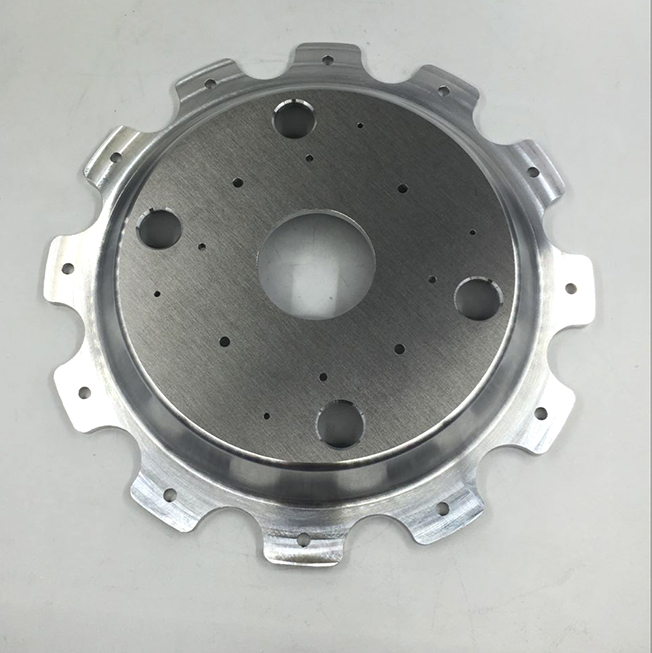
① لازم است از نیازهای مهارت برای پردازش قطعات و پردازش محصولات واجد شرایط اطمینان حاصل شود.
② منجر به بهبود نرخ تولید.
the هزینه های تولید (هزینه های پردازش) را تا حد امکان کاهش دهید.
2. تجزیه و تحلیل فناوری قطعات ماشینکاری CNC
تجزیه و تحلیل فنی ماشینکاری CNC شامل طیف گسترده ای از مناطق است ، بنابراین ما فقط آن را از دو جنبه امکان و راحتی ماشینکاری CNC تجزیه و تحلیل می کنیم.
(1) داده های مقیاس در نقاشی قسمت باید مطابق با اصل راحتی برنامه نویسی باشد
1. از روش نشانه ابعاد در نقاشی قسمت باید برای ویژگی های ماشینکاری CNC استفاده شود. در قسمت نقاشی ماشینکاری CNC ، مقیاس باید با همان داده نقل شود یا مقیاس مختصات باید مستقیماً داده شود. این روش مارک نه تنها برنامه نویسی را تسهیل می کند ، بلکه هماهنگی بین استانداردها را نیز تسهیل می کند و راحتی زیادی را در پیگیری سازگاری معیارهای طراحی ، معیارهای فرآیند ، معیارهای بازرسی و تنظیمات مبدا برنامه نویسی به ارمغان می آورد. از آنجا که طراحان بخش به طور کلی مونتاژ و سایر خصوصیات استفاده را در برچسب زدن در مقیاس در نظر می گیرند ، آنها باید روش های برچسب زدن جزئی را انتخاب کنند ، که باعث ایجاد ناراحتی زیادی برای پردازش سازمان و ماشینکاری CNC می شود. از آنجا که دقت ماشینکاری CNC و دقت موقعیت یابی مکرر بسیار زیاد است ، به دلیل خطاهای بزرگ تجمع ، ویژگی های استفاده آسیب نمی بیند ، بنابراین می توان بخشی از روش برچسب زدن پراکنده را به همان مقیاس استناد به مرجع تغییر داد یا روش برچسب زدن که مستقیماً مختصات را ارائه می دهد مقیاس واد
2. شرایط چندین عنصر که القاء بخشی را تشکیل می دهند باید کافی باشد
مختصات نقطه پایه یا گره باید در طول برنامه نویسی دستی محاسبه شود. در طول برنامه نویسی فعال ، تمام عناصر ژنومی که بخشی را تشکیل می دهند باید تعریف شوند. بنابراین ، هنگام تجزیه و تحلیل نقاشی قسمت ، لازم است تجزیه و تحلیل کند که آیا شرایط داده شده از عناصر معدود کافی است یا خیر. به عنوان مثال ، قوس و خط مستقیم ، قوس و قوس در نقاشی مماس هستند ، اما با توجه به مقیاس داده شده در نقاشی ، هنگامی که شرایط مماس محاسبه می شود ، به حالت تقاطع یا جداسازی تبدیل می شود. به دلیل شرایط ناکافی عناصر تشکیل دهنده ، شروع برنامه نویسی غیرممکن است. هنگام مواجهه با این وضعیت ، باید از طریق مشورت با طراح قسمت حل شود.
(2) ساختار و کاردستی هر قسمت پردازش از قسمت باید مطابق با ویژگی های ماشینکاری CNC باشد
1) بهتر است همان نوع و اندازه هندسه را برای حفره و شکل قطعات انتخاب کنید. این می تواند مشخصات ابزار و تعداد تغییرات ابزار را کاهش دهد ، برنامه نویسی را تسهیل کند و راندمان تولید را بهبود بخشد.
2) اندازه فیله شیار داخلی اندازه قطر ابزار را تعیین می کند ، بنابراین شعاع فیله شیار داخلی نباید خیلی کوچک باشد. پردازش قطعات مربوط به ارتفاع جمع فرآوری شده ، اندازه شعاع قوس انتقال و غیره است.
3) هنگامی که قسمت در حال حرکت به سمت پایین هواپیمای پایین است ، شعاع فیله پایین شیار نباید خیلی بزرگ باشد.
4) از موقعیت مرجع مداوم باید استفاده شود. در ماشینکاری CNC ، اگر موقعیت مرجع مداوم وجود نداشته باشد ، نصب مجدد قطعه کار باعث ناسازگاری در جهت گیری و مقیاس دو چهره پس از ماشینکاری می شود. بنابراین ، برای جلوگیری از بروز مشکلات فوق و اطمینان از صحت جهت گیری نسبی پس از دو فرآیند بستن ، باید یک موقعیت مرجع مداوم انتخاب شود.
بهتر است سوراخ های مناسب روی قطعات به عنوان سوراخ های مرجع موقعیت یابی داشته باشید. اگر اینگونه نباشد ، سوراخ های فرآیند را به عنوان سوراخ های مرجع موقعیت یابی تنظیم کنید (مانند اضافه کردن لبه های فرآیند روی خالی یا تنظیم سوراخ های فرآیند در حاشیه که در فرآیند بعدی آسیاب می شوند). اگر سوراخ فرآیند ایجاد نشود ، حداقل از ظاهر نهایی باید به عنوان یک معیار ثابت استفاده شود تا خطاهای ناشی از این دو بست را کاهش دهد. علاوه بر این ، همچنین باید تجزیه و تحلیل کند که آیا دقت ماشینکاری مورد نیاز و تحمل بعدی قطعات می تواند تضمین شود ، خواه ابعاد اضافی وجود داشته باشد که باعث تناقض می شوند یا ابعاد بسته ای که بر سازمان فرآیند تأثیر می گذارد.